The use of MIG in aircraft injectors connecting the turbocharger and exhaust pipe is a testament to the advancements in welding technology. In this context, MIG welding involves the utilization of a continuous solid wire electrode and a shielding gas to join two metal pieces seamlessly. This method provides a robust and efficient connection in the challenging aerospace environment.
When examining the intricacies of the MIG process in aircraft applications, it’s important to highlight the significance of the term inert gas. In welding, the inert gas serves as a shield to protect the weld pool from atmospheric contaminants, ensuring a clean and reliable bond between the turbocharger and the exhaust pipe. The use of MIG welding in this context enhances the durability and structural integrity of the connection, vital for the demanding conditions of aircraft operation.
Moreover, the choice of MIG in this specific application is influenced by its versatility and efficiency. The ability to maintain a stable arc, coupled with the continuous feed of the electrode, allows for precise control over the welding process. This is crucial when connecting the turbocharger and exhaust pipe, where precision is paramount to ensure optimal engine performance.
Examining the acronym MIG from a broader perspective in the aviation industry, it’s essential to recognize the role of this welding technique in fabricating various components. The adaptability of MIG welding makes it a preferred method for creating robust and reliable connections in aircraft structures, contributing to the overall safety and longevity of the vehicles.
Modern aircraft mig engines exhaust gas recirculation through turbocharger detailed explanation
Modern aircraft engines employ a sophisticated turbocharger system coupled with exhaust gas recirculation (EGR) to enhance efficiency and reduce environmental impact. This innovative approach involves redirecting a portion of the exhaust gases back into the engine through a series of intricate mechanisms.
The primary component driving this process is the turbocharger. Traditionally known for boosting engine performance by compressing air before it enters the combustion chamber, the turbocharger now plays a dual role in the context of EGR. In a typical configuration, a turbocharger consists of a turbine and a compressor connected by a shaft. The turbine is positioned in the exhaust stream, extracting energy from the hot gases, while the compressor pressurizes the incoming air.
The integration of EGR involves the introduction of a specialized valve, known as the EGR valve, strategically placed between the exhaust manifold and the turbocharger. This valve regulates the flow of exhaust gases that are redirected into the turbocharger system. The EGR gases are carefully mixed with the compressed air from the turbocharger before entering the combustion chamber.
The benefits of this approach are manifold. By introducing a controlled amount of EGR gases into the combustion process, temperatures within the engine are moderated, reducing the formation of harmful nitrogen oxides (NOx). This proves especially crucial in meeting stringent environmental regulations and ensuring aircraft engines adhere to emission standards.
Moreover, the integration of EGR through the turbocharger system contributes to improved fuel efficiency. The moderated temperatures and optimized air-fuel mixture result in more efficient combustion, translating to enhanced overall performance and reduced fuel consumption.
The operational dynamics involve a delicate balance. The EGR valve must be precisely controlled to maintain optimal combustion conditions. Advanced sensors and control systems continuously monitor parameters such as engine load, temperature, and altitude, adjusting the EGR flow accordingly.
In a simplified form, the EGR through turbocharger system can be visualized as a closed-loop process. The exhaust gases, instead of being released entirely into the atmosphere, are harnessed to enhance both environmental sustainability and the efficiency of the aircraft engine.
As aviation strives towards greener technologies, the integration of exhaust gas recirculation through the turbocharger system stands as a testament to the industry’s commitment to innovation and environmental responsibility.
What purpose serve so called mig rings visible on aircraft turbocharger housing
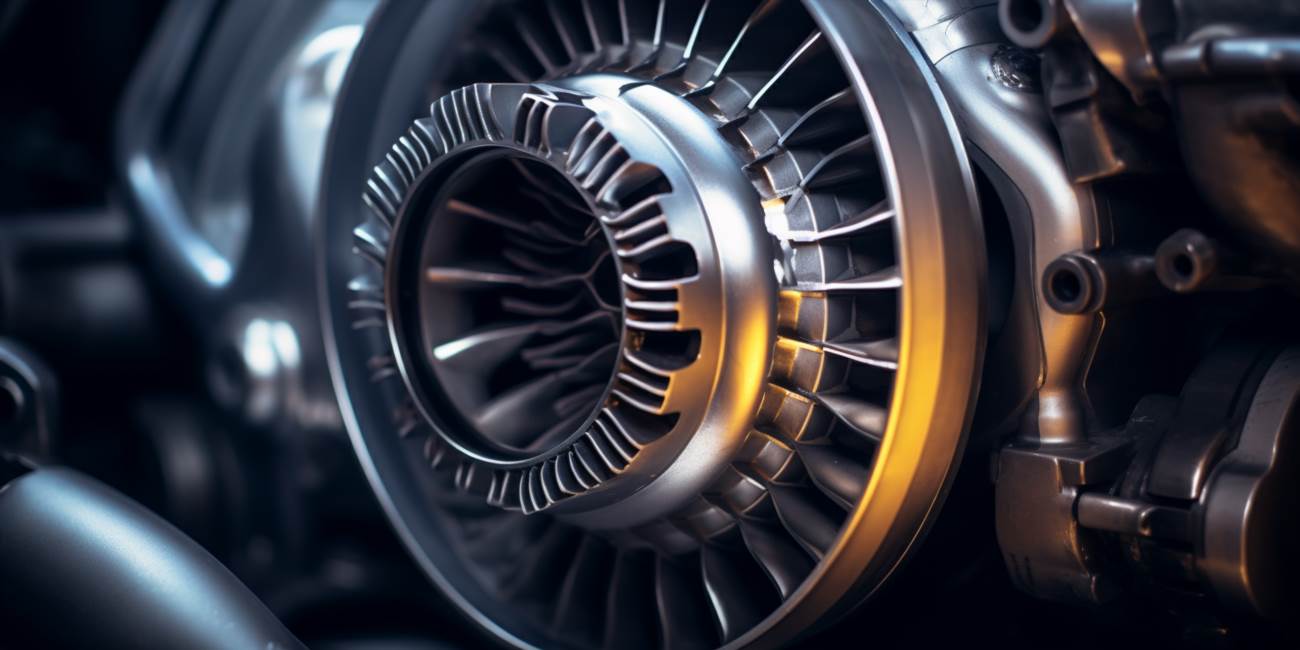
When it comes to the intricate world of aircraft turbochargers, one cannot overlook the significance of MIG rings. These small but mighty components play a crucial role in enhancing various aspects of turbocharger functionality, ultimately contributing to improved sealing, increased efficiency, and reduced leaking, resulting in an overall better performance.
Let’s delve into the specifics of how these MIG rings work their magic. One of their primary functions is to improve sealing within the turbocharger housing. As the turbocharger operates at high speeds, maintaining a tight seal is paramount to prevent any unwanted leakage. The precision and durability of MIG rings ensure a robust barrier, effectively containing the pressurized air within the turbocharger.
Moreover, the incorporation of MIG rings leads to a notable enhancement in turbocharger efficiency. By minimizing internal air leaks, these rings enable the turbocharger to operate at optimal levels. This means that a greater volume of air can be efficiently compressed, resulting in improved engine performance. The increase in efficiency directly translates to better fuel combustion and, subsequently, enhanced overall efficiency of the aircraft.
Now, let’s address the aspect of reducing leaking. The tight seal provided by MIG rings not only prevents air leakage but also contributes to the longevity of the turbocharger. Reduced wear and tear due to minimized leaks result in a more durable and reliable turbocharger system. This is a critical factor in ensuring the sustained performance of an aircraft over time.
As aviation technology continues to evolve, the role of MIG rings becomes increasingly vital in achieving better performance standards. Their meticulous design and functionality exemplify precision engineering at its finest. The aviation industry relies on these small yet powerful components to push the boundaries of what aircraft can achieve in terms of efficiency and reliability.
Why mig aircraft manufacturers started using stamped rings around turbocharger housing inlets
Modern aircraft engines have undergone significant advancements to enhance their efficiency and overall performance. One crucial innovation that has contributed to these improvements is the incorporation of stamped rings around turbocharger housing inlets. This engineering marvel serves multiple purposes, ranging from improving sealing to limiting exhaust bypass and ultimately increasing performance.
The utilization of stamped rings is rooted in the quest for airtight systems. These rings play a pivotal role in improving sealing around the turbocharger housing inlets. By creating a robust seal, they prevent unwanted air leakage, ensuring that the turbocharger operates within an optimal environment. This enhanced sealing not only contributes to the longevity of the engine but also plays a crucial role in maintaining consistent performance.
One of the primary challenges in aircraft engines is the potential for leaks, which can significantly impact efficiency. The introduction of stamped rings addresses this concern by providing an additional layer of protection against leaks. These rings act as a barrier, reducing leaks to a minimum and enhancing the overall reliability of the turbocharging system.
Besides improving sealing and reducing leaks, the use of stamped rings contributes to better turbocharging. Turbochargers play a crucial role in increasing the airflow into the engine, thereby improving combustion efficiency. The stamped rings optimize this process by ensuring that the turbocharger operates at peak performance, leading to better turbocharging overall.
Furthermore, these rings play a vital role in limiting exhaust bypass. Uncontrolled exhaust bypass can negatively impact the performance of the turbocharger. The stamped rings act as a containment mechanism, directing the exhaust gases precisely where they are needed for optimal turbocharging. This precision in controlling the exhaust flow contributes to the increase in performance observed in modern aircraft engines.