The aviation industry is a realm where every ounce matters, and 400Hz frequency provides a sweet spot for balancing power requirements with weight considerations. Higher frequencies allow for the design of smaller and lighter transformers and motors, a paramount concern when soaring through the skies where fuel efficiency is paramount.
Imagine an aircraft as a symphony of electrical components, each playing its unique role. 400Hz orchestrates this symphony with finesse. It allows for the downsizing of components like transformers and generators, reducing the overall weight of the aircraft. In the high-altitude dance of flight, every pound shed contributes to fuel savings and increased performance.
Additionally, 400Hz proves to be a virtuoso in the realm of inductive reactance. The higher frequency reduces the size of inductive components, making them more responsive to rapid changes in current. This characteristic is crucial for avionics, where swift and precise electrical responses are imperative for the safety and functionality of various systems.
Let’s delve into the technical intricacies. The aircraft’s power distribution system relies on 400Hz alternating current (AC). This choice is not arbitrary; it is a calculated decision to balance the advantages of high frequency with the practical aspects of electrical systems in flight. The aviation engineers have orchestrated a delicate ballet of efficiency and performance.
Consider the aviation landscape as a canvas, with each stroke of engineering precision contributing to the masterpiece of flight. 400Hz emerges as a stroke that defines efficiency, enabling the aircraft to cut through the air with grace and precision.
As we navigate the skies, the use of 400Hz in aircraft becomes a testament to the meticulous planning and engineering prowess that propels us into the future of aviation. It’s not just a frequency; it’s a choice that echoes through the wings and fuselage, a choice that defines the very essence of flight.
Advantages of using 400 hz frequency in aircraft electrical systems
In the realm of aircraft electrical systems, the utilization of 400 Hz frequency brings forth a multitude of advantages, contributing to enhanced performance, efficiency, and safety. This higher frequency, compared to the more conventional 60 Hz used in residential and commercial applications, offers several distinctive benefits in the aviation domain.
The primary advantage lies in the size and weight reduction of electrical components. At 400 Hz, transformers and inductors can be significantly smaller and lighter compared to their 60 Hz counterparts. This reduction in size is crucial for aircraft, where every kilogram matters. The aerospace industry constantly strives to optimize weight, as it directly correlates with fuel efficiency and overall operational costs.
Another noteworthy benefit is the improved power distribution capabilities provided by 400 Hz systems. The higher frequency allows for more efficient transmission of electrical power over longer distances. This efficiency is particularly advantageous in the extensive wiring systems of aircraft, minimizing power losses and ensuring a reliable supply of electricity to various onboard systems.
The compatibility with avionic equipment is a key factor in the widespread adoption of 400 Hz frequency. Many avionic devices, such as radars and navigation systems, are designed to operate optimally at 400 Hz. This compatibility ensures seamless integration and optimal performance of critical aircraft systems, contributing to overall operational reliability.
Furthermore, the reduced electromagnetic interference (EMI) is a crucial aspect of 400 Hz systems. The higher frequency allows for more efficient filtering of unwanted electromagnetic signals, reducing the likelihood of interference with sensitive avionic equipment. This is paramount for ensuring accurate communication and operation of navigation and communication systems in the aircraft.
When it comes to motor-driven components like pumps and fans, 400 Hz systems exhibit a distinct advantage. Motors operating at this frequency can be smaller and lighter while maintaining the same power output. This is a significant factor in the design of various aircraft systems, where space and weight considerations are critical.
To illustrate the advantages of 400 Hz frequency in a more structured manner, consider the following table:
Advantage | Description |
---|---|
Size and Weight Reduction | Significantly smaller and lighter electrical components. |
Improved Power Distribution | Efficient transmission of power over longer distances, minimizing losses. |
Compatibility with Avionic Equipment | Optimal performance of critical systems designed for 400 Hz operation. |
Reduced Electromagnetic Interference | Efficient filtering of unwanted signals, ensuring reliable communication and operation. |
Advantage for Motor-Driven Components | Smaller and lighter motors with the same power output. |
Summarily, the adoption of 400 Hz frequency in aircraft electrical systems is a strategic choice, offering a harmonious blend of size and weight efficiency, improved power distribution, compatibility with avionic equipment, reduced electromagnetic interference, and advantages for motor-driven components.
How 400 hz helps reduce interference and improve reliability in aircraft
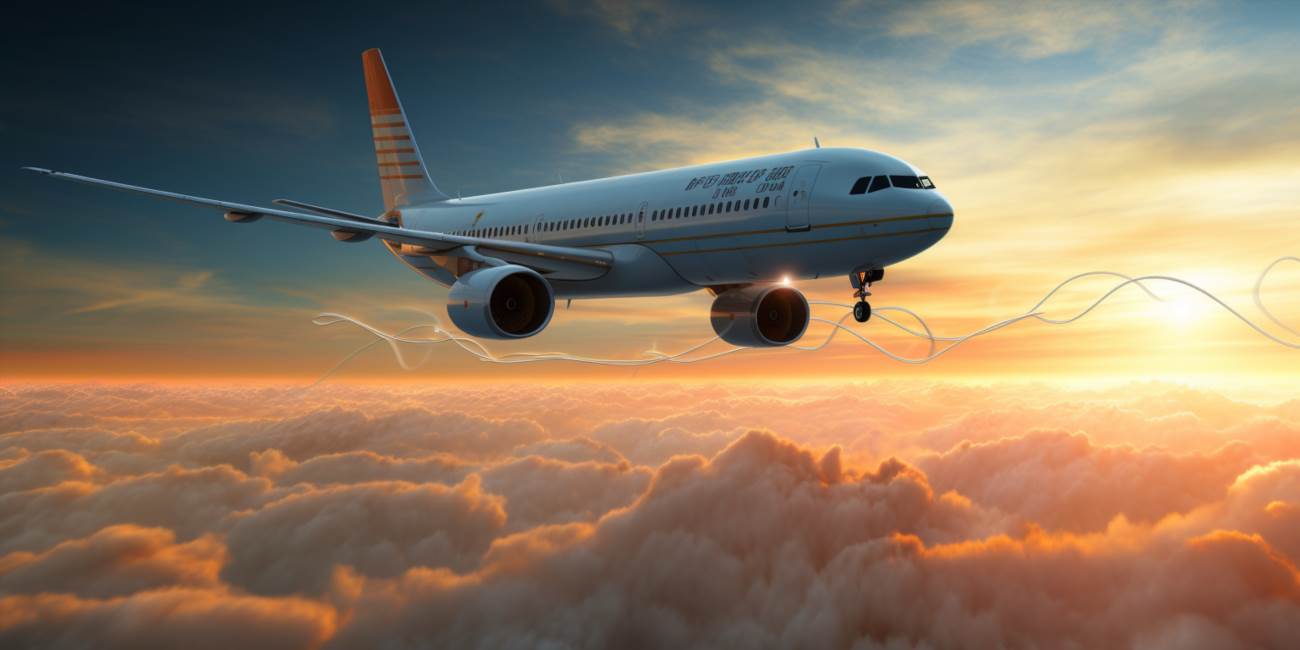
The use of 400 Hz power systems in aircraft plays a pivotal role in enhancing both reliability and safety. This higher frequency is advantageous for several reasons, notably in noise isolation and corrosion prevention.
One of the primary benefits of employing a 400 Hz power system is its contribution to noise isolation. In aviation, where the reduction of noise is critical for both crew and passenger well-being, a higher frequency power supply enables smaller and lighter transformers. These transformers are more efficient at handling power conversion, resulting in less heat dissipation and consequently, reduced acoustic emissions. The ability to isolate and mitigate noise is imperative for creating a more comfortable and safer in-flight environment.
Moreover, the 400 Hz power system aids in corrosion prevention. Aircraft are subjected to various environmental factors, including moisture and corrosive agents. The higher frequency power systems allow for the use of smaller and lighter wiring, which, in turn, reduces the chances of corrosion. Additionally, the increased frequency enhances the efficiency of various systems, reducing the overall power consumption and, consequently, minimizing the heat generated. This reduction in heat is instrumental in preventing corrosion, as it limits the conditions conducive to oxidation and rust formation.
When considering the aircraft’s electrical system, the use of 400 Hz power is not just about noise and corrosion—it also significantly contributes to overall system reliability. The higher frequency allows for more efficient power distribution, enabling the use of smaller and lighter cables without compromising performance. This, in turn, leads to a reduction in the overall weight of the aircraft, enhancing fuel efficiency and operational economy.
In terms of safety and reliability, the 400 Hz power systems are less prone to interference. This is particularly crucial in modern aircraft, where a myriad of electronic systems coexists. The higher frequency minimizes electromagnetic interference, ensuring that critical avionics systems operate without disruptions. Additionally, the improved power quality contributes to the longevity and stability of sensitive electronic components, further reinforcing the aircraft’s reliability.
Summarily, the adoption of 400 Hz power systems in aircraft is a strategic decision to improve various facets of aviation, from enhancing noise isolation for a more comfortable journey to aiding in corrosion prevention for increased longevity. Beyond these advantages, the higher frequency power systems fortify the overall reliability and safety of modern aircraft, paving the way for more efficient and secure air travel.
Historical background of adopting 400 hz standard for aircraft
The adoption of the 400 Hz standard in aircraft power systems has a fascinating historical background deeply rooted in the evolution of aviation technology. In the early days of aviation, aircraft electrical systems operated at lower frequencies, typically around 60 Hz. However, as aircraft technology advanced, the need for more efficient and lighter electrical systems became apparent.
The shift towards the 400 Hz standard can be traced back to the mid-20th century when the aviation industry witnessed a surge in the development of more sophisticated and electronic equipment onboard. The higher frequency offered several advantages, most notably the reduction in the size and weight of transformers and other components.
One crucial aspect of aircraft power systems influenced by the 400 Hz standard is the concept of power factor. In alternating current (AC) circuits, the power factor is the ratio of real power to apparent power. Maintaining a high power factor is essential for efficient power transmission and distribution.
With the adoption of the 400 Hz standard, aircraft power systems benefit from an improved power factor. The higher frequency allows for the design of lighter and more compact components, contributing to the overall efficiency of the electrical system. This is particularly crucial in aviation, where every pound of weight saved translates into fuel efficiency and increased payload capacity.
Brushless generators play a pivotal role in the aircraft power systems adhering to the 400 Hz standard. These generators eliminate the need for brushes and commutators, offering advantages such as reduced maintenance requirements and increased reliability. The elimination of these components also contributes to a more streamlined design, aligning with the aviation industry’s constant pursuit of weight reduction.
Compared to traditional brushed generators, brushless generators exhibit a higher level of efficiency and durability. The absence of brushes reduces friction and wear, leading to longer operational lifespans and fewer instances of component failure. These characteristics make brushless generators well-suited for the demanding and critical requirements of aircraft power systems.