For instance, a smaller piston engine, commonly found in light aircraft, may have a more affordable upfront cost ranging from tens to hundreds of thousands of dollars. On the other hand, high-performance jet engines, prevalent in commercial airliners, can soar into the millions. The complexity, efficiency, and technology incorporated into these engines heavily influence their price.
However, the cost of an aircraft engine doesn’t conclude with the initial purchase. Maintenance and operation expenses are significant considerations. Aircraft engines, subjected to extreme conditions and high stress during flights, demand meticulous maintenance to ensure optimal performance and longevity. Regular inspections, repairs, and overhauls contribute to the overall cost of owning and operating an aircraft engine.
Maintenance activities are often scheduled based on the number of hours an engine has been in operation. This preventive approach helps identify and rectify potential issues before they escalate, reducing the risk of catastrophic failure and mitigating long-term costs.
Moreover, the operating costs of an aircraft engine include fuel consumption, which can vary depending on the type of engine and the efficiency of its design. Modern engines are designed with fuel efficiency in mind, aligning with the aviation industry’s growing focus on environmental sustainability.
Let’s break down the key points:
Aspect | Details |
---|---|
Initial Cost | The price of aircraft engines ranges from thousands to millions, contingent on size and capabilities. |
Maintenance | Maintenance is crucial for optimal performance, requiring regular inspections and repairs. |
Operating Costs | Operating costs encompass fuel consumption, influenced by engine type and design efficiency. |
The initial price of aircraft engines and what impacts it
Aircraft engines, the beating hearts of flying machines, come with a price tag that reflects not only their complexity but also a myriad of factors that influence their initial cost. Understanding these factors is crucial for aviation enthusiasts, industry professionals, and anyone intrigued by the intricate world of aviation technology.
The manufacturing complexity of aircraft engines plays a pivotal role in determining their initial price. Modern engines are marvels of engineering, featuring cutting-edge materials, advanced manufacturing processes, and intricate designs. The use of lightweight yet durable materials, such as composite alloys and high-strength titanium, adds to both the performance and cost of these engines. The more sophisticated the materials and manufacturing techniques, the higher the initial price of the engine.
Another significant factor influencing the cost of aircraft engines is the technological advancements incorporated into their design. Engines equipped with state-of-the-art technologies, such as adaptive fan systems, integrated sensors, and fuel-efficient technologies, command a higher price due to the research, development, and implementation costs associated with these innovations. These cutting-edge features not only enhance performance but also contribute to the overall efficiency and sustainability of the aircraft.
Market demand is a key player in determining the initial price of aircraft engines. When demand outstrips supply, manufacturers can adjust prices accordingly. The aviation industry’s cyclical nature, influenced by economic conditions and geopolitical factors, can lead to fluctuations in demand. Engine manufacturers need to balance their production capacities with market demand to maintain competitiveness without compromising quality.
The size and power of an aircraft engine significantly impact its cost. Larger engines with higher thrust capabilities, often required for wide-body or long-range aircraft, entail more extensive engineering and material costs. The power output, measured in terms of thrust or horsepower, directly correlates with the size and complexity of the engine. Engines designed for smaller aircraft may be more economical due to their reduced size and power requirements.
Environmental considerations, such as emission standards and fuel efficiency regulations, also contribute to the pricing of aircraft engines. Manufacturers investing in environmentally friendly technologies and meeting stringent emission standards may incur additional costs, which are then reflected in the engine’s price. This reflects the industry’s commitment to sustainability and aligning with global efforts to reduce the environmental impact of air travel.
Operating costs and required maintenance for airplane powerplants
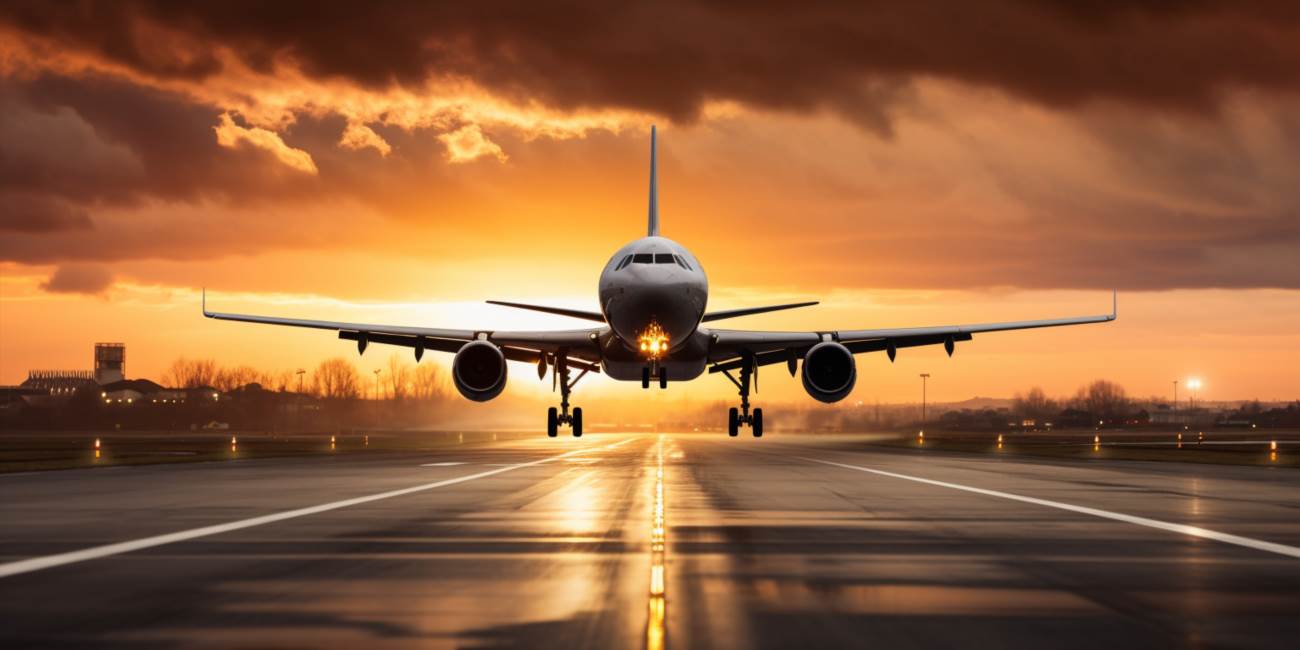
Operating an aircraft efficiently involves careful consideration of fuel consumption and the associated costs. The powerplants of airplanes play a crucial role in this aspect. These engines are not only the heart of flight but also significant contributors to operational expenses.
The fuel consumption of airplane powerplants is a critical factor in determining overall operating costs. Modern engines are designed with a focus on fuel efficiency, utilizing advanced technologies to optimize combustion processes. This results in reduced fuel consumption per flight hour, translating into cost savings for airlines.
Regular inspection and maintenance are essential to ensure the continued reliability and efficiency of airplane powerplants. Scheduled inspections involve a comprehensive assessment of engine components, identifying any wear and tear that may affect performance. Addressing these issues proactively during routine inspections helps prevent more significant problems and costly repairs in the long run.
Overhauling an aircraft engine is a meticulous process that aims to extend its lifespan and maintain optimal performance. This involves disassembling the engine, inspecting each part thoroughly, and replacing or repairing components as necessary. An overhaul is a substantial investment but is a cost-effective approach compared to dealing with unexpected failures that can occur without proper maintenance.
When it comes to repair of airplane powerplants, timely action is crucial. Even with regular maintenance, unexpected issues may arise, necessitating immediate attention. Airlines and maintenance crews must have a robust system in place to address these repair needs promptly, minimizing downtime and ensuring the safety and reliability of the aircraft.
Effective management of operating costs for airplane powerplants involves a delicate balance between routine maintenance, addressing unexpected issues through timely repair, and strategically planning engine overhaul based on manufacturer recommendations. This approach not only enhances the overall efficiency of the aircraft but also contributes to the airline’s bottom line.
Aspect | Importance |
---|---|
Fuel Consumption | Crucial for determining overall operating costs; modern engines focus on fuel efficiency. |
Inspection | Regular assessments to identify and address potential issues proactively. |
Overhaul | Meticulous process to extend engine lifespan and maintain optimal performance. |
Repair | Timely action to address unexpected issues, ensuring safety and reliability. |
Useful life and durability of aviation power plants
Aviation power plants are marvels of engineering, exemplifying longevity, endurance, sturdiness, and wear resistance. These complex systems undergo rigorous testing and scrutiny to ensure they can withstand the harsh conditions of the skies.
One of the key factors contributing to the longevity of aviation power plants is meticulous design. Engineers employ cutting-edge materials and technologies to create components that can withstand the test of time. The use of advanced alloys and composites enhances the overall sturdiness of these power plants, allowing them to endure the demanding operational environments they encounter.
When it comes to endurance, aviation power plants are designed to operate seamlessly over extended periods. Continuous advancements in propulsion technologies contribute to increased fuel efficiency, reducing the strain on these power plants during long-haul flights. This focus on efficiency not only enhances endurance but also plays a crucial role in minimizing environmental impact.
Moreover, wear and tear are inevitable in any mechanical system, but aviation power plants are engineered with a keen emphasis on wear resistance. Critical components such as turbine blades and bearings undergo specialized treatments and coatings to mitigate the effects of friction and abrasion, ensuring a prolonged and reliable service life.
In the realm of aviation, safety is paramount. The sturdiness of power plants is rigorously tested under extreme conditions, from temperature variations to intense vibrations. These tests not only validate the structural integrity but also contribute to the overall endurance of the power plant, assuring operators and passengers alike that these systems can withstand the challenges of diverse flight scenarios.
Furthermore, ongoing research and development in the aviation industry aim to enhance the longevity of power plants through innovations like predictive maintenance. By leveraging advanced sensors and analytics, operators can proactively address potential issues, extending the lifespan of critical components and ensuring the continued endurance of aviation power plants.