Welding careers have evolved beyond the stereotype of a gritty workshop to encompass cutting-edge industries like aerospace. The fusion of skilled craftsmanship and technological innovation has propelled aircraft welding into a realm of high demand.
Aircraft welders find themselves at the heart of building, repairing, and maintaining aircraft structures. This includes crucial components like wings, fuselage, and landing gear. The precision required in aerospace welding is unparalleled, making it a niche but indispensable skill set.
Now, let’s address the elephant in the room – salary. The compensation for aircraft welders is notably higher than their counterparts in more conventional welding fields. The intricate nature of the work, coupled with stringent quality standards, commands a premium.
According to industry reports, the median annual salary for aircraft welders hovers around $60,000 to $70,000. However, it’s essential to note that experience, location, and employer play pivotal roles in determining the paycheck. Those with a robust track record and specialized certifications may even breach the $80,000 mark.
The aerospace industry’s continuous growth fuels the job outlook for aircraft welders. As air travel becomes more integral to global connectivity, the demand for skilled professionals who can ensure the structural integrity of aircraft is on a steady ascent.
Now, let’s highlight some key factors that contribute to the salary variation within this domain. Geographic location is a significant player – regions with a higher cost of living often offer more substantial compensation packages. Additionally, the type of aircraft being worked on and the complexity of the welding required can influence earnings.
It’s not just about the paycheck; aircraft welders often enjoy a sense of accomplishment, knowing their work is fundamental to aviation safety. This intrinsic motivation, combined with the tangible benefits, makes this career choice appealing to those with a passion for precision engineering.
Aircraft welding career guide: training, jobs and salary
Embarking on a career in aircraft welding can be a thrilling journey filled with opportunities for growth and expertise. The field demands a unique set of skills and knowledge, making it essential for aspiring aircraft welders to undergo specialized training programs to ensure they are well-equipped for the challenges ahead.
One of the critical aspects of a successful career in aircraft welding is acquiring the necessary technical skills. This involves proficiency in various welding techniques such as gas tungsten arc welding (GTAW), gas metal arc welding (GMAW), and shielded metal arc welding (SMAW). A comprehensive training program should cover these techniques, ensuring welders can adapt to the diverse needs of the aerospace industry.
Moreover, an understanding of blueprints and technical drawings is indispensable. Aircraft welders must be able to interpret complex schematics and translate them into precise and accurate welds. This skill is honed through both theoretical learning and hands-on practice, allowing welders to navigate the intricate details of aircraft structures.
Once the training is complete, the next step is to explore the myriad of job opportunities in the aerospace sector. Aircraft welders can find employment in various settings, including aircraft manufacturing facilities, repair and maintenance workshops, and even within government agencies overseeing aviation safety. The demand for skilled aircraft welders is high, offering a broad spectrum of choices for professionals in this field.
When it comes to salary expectations, aircraft welding can be a lucrative career path. The average annual salary for aircraft welders in the United States, for example, is around $60,000 to $80,000, depending on experience and expertise. Specializations in specific areas, such as working on military aircraft or commercial jets, can also impact salary levels.
It’s important to note that continuous learning is key to excelling in this field. Staying updated with the latest welding technologies, materials, and industry standards is crucial for career advancement. Many aircraft welders pursue certifications from reputable organizations to validate their skills and enhance their marketability.
What does an aircraft welder do: responsibilities and skills
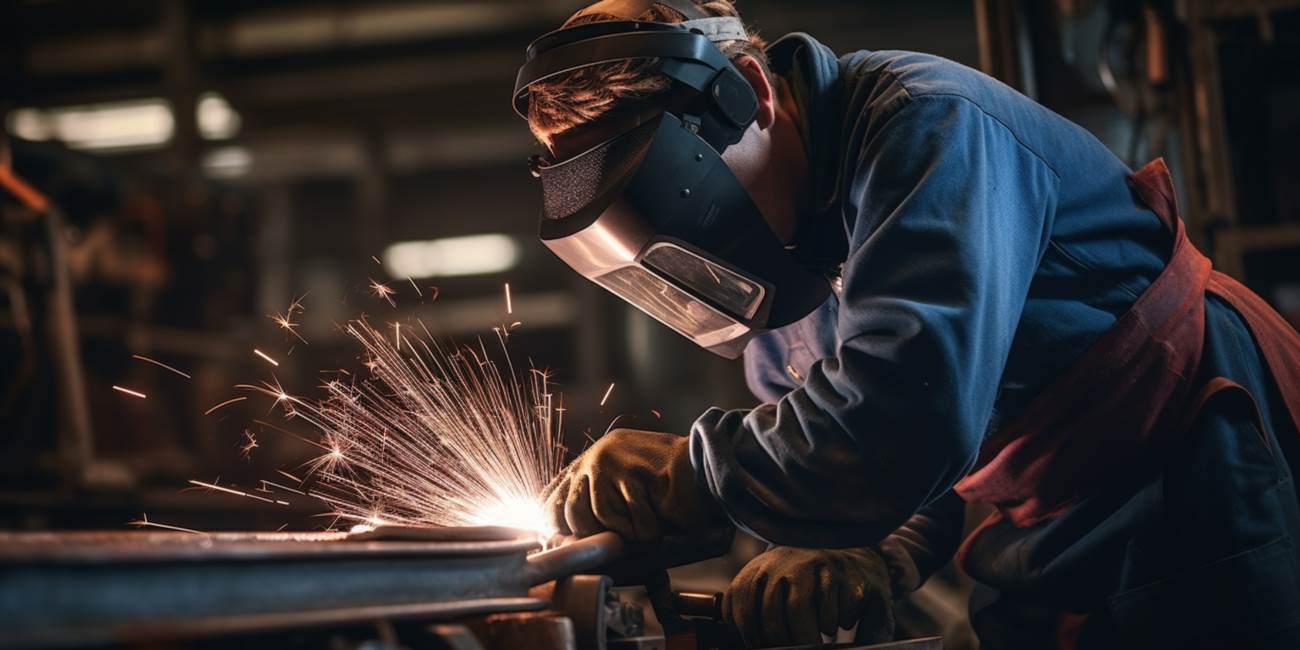
An aircraft welder plays a crucial role in the aviation industry, contributing to the fabrication and maintenance of aircraft components. These skilled professionals are responsible for performing welding tasks on various parts of an aircraft, ensuring structural integrity and safety.
The responsibilities of an aircraft welder involve working with a variety of materials, including aluminum and titanium, to create strong and durable joints. They interpret engineering drawings and blueprints, determining the precise specifications for each weld. Precision is paramount, as even a minor error can have severe consequences in aviation.
When it comes to skills, aircraft welders need a deep understanding of metallurgy and welding techniques. They must be proficient in using various welding equipment, such as TIG and MIG welders. Attention to detail is a must, coupled with the ability to work in confined spaces, as aircraft components often have tight quarters that require intricate welding work.
As for the salary, aircraft welders are typically well-compensated for their specialized skills. The median annual salary for these professionals falls within the range of $50,000 to $70,000, with factors like experience, location, and the employer influencing the exact compensation.
Looking at the job outlook, the aviation industry’s growth directly impacts the demand for skilled aircraft welders. As air travel continues to expand globally, there is a sustained need for professionals who can maintain and repair aircraft components. This positive job outlook suggests that pursuing a career as an aircraft welder could lead to long-term employment opportunities.
When it comes to working on aviation parts, aircraft welders focus on a wide range of components, from the fuselage to engine parts. They may be involved in the production of new aircraft or repairing and maintaining existing ones. The ability to adapt to different tasks and understand the unique requirements of each aviation part is a vital aspect of the job.
How to become an aircraft welder: education and certification
To become an aircraft welder, individuals need a combination of education and certification, specialized training programs, and mastery of advanced welding techniques tailored to the demands of the airline industry.
Firstly, aspiring aircraft welders must acquire a strong educational foundation. While a high school diploma is the minimum requirement, pursuing post-secondary education in welding or a related field is highly beneficial. Enrolling in vocational schools, community colleges, or specialized institutions offering welding programs provides the necessary theoretical knowledge.
Obtaining relevant certifications is crucial in the aerospace welding field. The American Welding Society (AWS) provides various certifications, including Certified Welder (CW) and Certified Welding Inspector (CWI), both widely recognized in the industry. These certifications validate the welder’s skills and ensure compliance with industry standards.
Specialized training programs play a pivotal role in shaping the expertise of aircraft welders. These programs, often offered by aviation maintenance schools or welding institutes, focus on the intricacies of welding within the aviation context. Rigorous hands-on training is provided to hone skills in precision welding, blueprint reading, and interpreting aircraft specifications.
One notable training initiative is the Federal Aviation Administration (FAA) Airframe and Powerplant (A&P) certification. While not solely focused on welding, it covers the broader spectrum of aircraft maintenance, including welding processes. This certification is highly regarded within the airline industry, opening doors to diverse opportunities.
When delving into welding techniques, aircraft welders must master both traditional and advanced methods. Gas tungsten arc welding (GTAW) and resistance spot welding are commonly used techniques due to their precision and suitability for aircraft materials. The ability to weld various materials, including aluminum and titanium, is imperative for success in the aerospace field.
Understanding the unique challenges posed by working on aircraft, such as confined spaces and intricate designs, is essential. Aircraft welders must demonstrate proficiency in structural welding, ensuring the integrity and safety of critical components like fuselage and engine parts.
The airline industry demands not only technical excellence but also adherence to strict safety and quality standards. Aircraft welders often work closely with aviation engineers and inspectors, necessitating effective communication skills to interpret complex specifications accurately.