One of the primary factors influencing the center of gravity is the distribution of the aircraft’s components, including its engines, fuel tanks, and payload. The location of these elements significantly impacts the center of gravity, and any changes in weight distribution can alter the aircraft’s overall balance.
Weight is a critical consideration when assessing the center of gravity. Variations in the aircraft’s overall weight can result from factors such as fuel consumption during flight or changes in the passenger and cargo load. Pilots and engineers must monitor these weight fluctuations to ensure that the center of gravity remains within safe limits.
Another factor influencing the center of gravity is the positioning of the aircraft’s control surfaces. The elevator, ailerons, and rudder all contribute to the overall balance of the aircraft. Adjusting these control surfaces can have a direct impact on the center of gravity, influencing the aircraft’s pitch, roll, and yaw characteristics.
Moreover, the design of the aircraft itself plays a significant role in determining its center of gravity. The distance between the wings, the length of the fuselage, and the tail configuration all contribute to the overall geometry that affects the center of gravity. Engineers carefully consider these design elements to optimize the aircraft’s performance.
It’s essential to note that pilots must adhere to specific limitations regarding the center of gravity established by the aircraft manufacturer. Deviating from these limitations can lead to stability issues and compromise the safety of the flight. Pilots use graphs and charts provided in the aircraft’s manual to determine the allowable center of gravity range based on the current weight and configuration.
Center of gravity shifts due to fuel consumption and payload changes
When it comes to aviation, the concept of center of gravity plays a crucial role in ensuring the stability and performance of an aircraft. The center of gravity (CG) is the point where the entire weight of the aircraft is considered to be concentrated. Any imbalance in the distribution of weight around this point can have significant implications for the aircraft’s handling.
One of the factors that can influence the center of gravity is the consumption of fuel during a flight. As an aircraft burns fuel, its overall weight decreases, leading to a shift in the center of gravity. Pilots and aircraft systems must constantly monitor fuel levels and make adjustments to ensure that the center of gravity remains within specified limits.
The relationship between fuel consumption and center of gravity is dynamic, requiring precise calculations and real-time adjustments. Modern aircraft are equipped with sophisticated computerized systems that continuously analyze fuel levels and make recommendations to the flight crew for optimal weight distribution.
Additionally, the payload of an aircraft, including passengers, cargo, and baggage, also contributes to the overall weight distribution. Loading and unloading of passengers and cargo can result in a shift in the center of gravity. Airlines and ground crews follow strict guidelines to ensure that the aircraft is loaded in a way that maintains a stable center of gravity.
It’s worth noting that the center of gravity is a critical consideration during the design phase of an aircraft. Engineers meticulously plan the placement of components, fuel tanks, and cargo holds to achieve a stable and predictable center of gravity under various operating conditions.
For a deeper understanding, consider the following scenario: imagine an aircraft taking off with a full tank of fuel and a maximum payload. As the flight progresses and fuel is consumed, the aircraft becomes lighter. The challenge is to manage this changing weight distribution to prevent the center of gravity from moving outside the acceptable range.
Visualizing these weight dynamics can be facilitated with the use of a table detailing the initial and final weights of the aircraft components, including fuel, passengers, and cargo. This table can illustrate how changes in each component impact the overall center of gravity.
Component | Initial Weight | Final Weight |
---|---|---|
Fuel | XX,XXX lbs | XX,XXX lbs |
Passengers | XX,XXX lbs | XX,XXX lbs |
Cargo | XX,XXX lbs | XX,XXX lbs |
Effective management of the center of gravity is essential for safe and efficient flight operations. Pilots, engineers, and ground crews work collaboratively to navigate the dynamic challenges posed by fuel consumption and payload changes, ensuring that the aircraft remains balanced and responsive throughout its journey.
Center of gravity calculation factors to consider
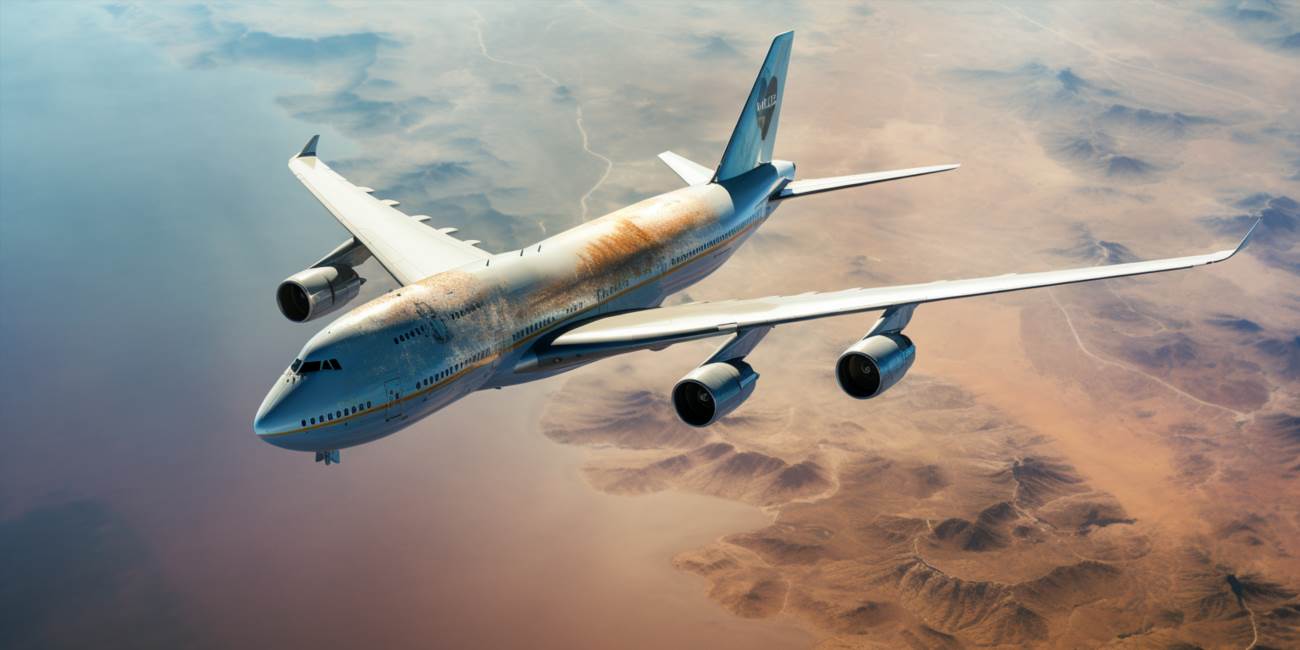
When delving into the intricate process of center of gravity calculation for aircraft, it’s crucial to take into account various calculation factors that directly influence the overall stability and performance. One of the primary considerations is the position of the aircraft’s components, with special attention to the position of the fuel systems.
The center of gravity is the point where the entire weight of the aircraft is concentrated, and achieving the right balance is paramount for safe and efficient flight. In the realm of calculation factors, the position of key components such as engines, wings, and tail plays a pivotal role. Any deviation from the optimal position can lead to imbalances that affect the aircraft’s handling and maneuverability.
Specifically, when it comes to the fuel systems, their position is a critical element in the center of gravity calculation. The distribution of fuel throughout the aircraft can vary during flight due to consumption, and this dynamic aspect must be factored into the overall calculation. Engineers meticulously analyze how the position of the fuel systems changes under different fuel loads and flight conditions.
Moreover, the weight and density of fuel are significant calculation factors. The quantity of fuel on board, its distribution, and how it shifts during flight impact the center of gravity. Engineers use sophisticated algorithms and mathematical models to predict these changes accurately, ensuring that the calculation remains precise even in dynamic situations.
Integrating these calculation factors requires a comprehensive understanding of the aircraft’s design and specifications. The position of heavy components like engines and the varying position of the fuel systems demand meticulous analysis. Engineers often create detailed charts and diagrams to visualize how changes in weight distribution influence the center of gravity, allowing for precise adjustments to maintain optimal balance.
In essence, the calculation factors for determining the center of gravity are a multidimensional puzzle where the position of critical components, including the dynamic position of the fuel systems, must be considered holistically. Achieving the perfect balance is not just a mathematical exercise but an art that ensures the aircraft’s stability and safety throughout its journey.
How weight distribution factors into center of gravity constraints
When delving into the intricacies of aviation, understanding the weight distribution becomes paramount, as it significantly influences the center of gravity (CoG). The center of gravity is a crucial concept in aircraft design and operation, dictating the equilibrium point where the aircraft’s mass is evenly distributed in all directions.
One of the primary considerations in aviation design is the adherence to weight cargo constraints. These constraints are stringent limits imposed on the total weight an aircraft can carry, encompassing both passengers and cargo. Violating these constraints can lead to a multitude of issues, including compromised structural integrity and impaired flight performance.
As aircraft are meticulously engineered to operate within specified g limits, the distribution of weight plays a pivotal role. The g limits, denoting the maximum load factor an aircraft can sustain, are contingent on the distribution of weight across its structure. Failure to adhere to these limits could result in structural failure or, conversely, limit the aircraft’s maneuverability.
The intricacies of weight distribution intertwine with the aircraft’s structural design. Ensuring that the mass is distributed appropriately is not solely about complying with weight cargo constraints; it also involves considering the aerodynamic implications. Engineers meticulously calculate the position of the center of gravity to guarantee optimal performance under various flight conditions.
To visualize the impact of weight distribution, consider the analogy of a seesaw. The seesaw, akin to an aircraft, relies on a balanced distribution of weight to maintain equilibrium. Similarly, an aircraft’s center of gravity must align with its g limits and weight cargo constraints to ensure stability and safe operation.
Practical solutions often involve employing sophisticated computer simulations and mathematical models. Engineers engage in a delicate dance of adjusting cargo placement, fuel distribution, and other variables to achieve the delicate equilibrium required for safe and efficient flight. This meticulous attention to detail is essential for meeting not only regulatory constraints but also for optimizing fuel efficiency and overall performance.