The empennage serves several essential functions. Firstly, it provides stability by counteracting the destabilizing forces that occur during flight. The horizontal stabilizer, typically located at the tail’s rear, prevents the aircraft from pitching excessively. This prevents abrupt changes in the aircraft’s attitude, ensuring a smooth and controlled flight experience for passengers and crew.
Understanding what is empennage in aircraft involves recognizing its role in controlling the aircraft’s yaw and roll. The vertical stabilizer, attached to the aircraft’s tail, houses the rudder, which is responsible for controlling yaw – the side-to-side movement of the aircraft. This is crucial for maintaining a straight and steady course, especially during adverse weather conditions or turbulence.
The elevators, located on the trailing edge of the horizontal stabilizer, are integral to controlling the aircraft’s pitch. These movable surfaces allow the pilot to adjust the aircraft’s nose up or down, influencing its ascent or descent. This control over pitch is vital for achieving a desired altitude and a smooth transition between different phases of flight.
In essence, the empennage acts as the aircraft’s tail-based command center, where intricate movements of its components translate into precise control over its orientation and direction. The design and configuration of the empennage are carefully engineered to optimize these control functions while minimizing drag and maximizing fuel efficiency.
Moreover, the empennage is subject to rigorous aerodynamic considerations. Engineers meticulously design its surfaces to ensure that airflow over and around the tail section remains predictable and manageable. This not only enhances the aircraft’s performance but also contributes to fuel efficiency, a critical factor in modern aviation.
As aviation technology advances, so does the refinement of empennage designs. Advanced materials, computer-aided simulations, and real-world testing contribute to the continuous improvement of this essential aircraft component. Pilots rely on the empennage for responsive and predictable control, especially during critical phases of flight such as takeoff, landing, and maneuvers.
Key parts that make up an aircraft’s empennage for stability and control
The empennage of an aircraft is a critical component that plays a pivotal role in providing stability and control during flight. Comprising various key parts, the empennage ensures the aircraft’s equilibrium and maneuverability in the skies.
One of the primary elements of the empennage is the vertical stabilizer. This upright structure, typically located at the rear of the aircraft, prevents unnecessary yawing or side-to-side motion. It acts as a stabilizing force, counteracting any disturbances that may affect the aircraft’s heading. The rudder is attached to the vertical stabilizer and is a movable control surface that enables the pilot to initiate yawing motions, maintaining directional control.
Adjacent to the vertical stabilizer, the horizontal stabilizer plays a crucial role in maintaining pitch stability. It consists of a fixed horizontal surface with an attached elevator, a movable control surface. The elevator allows the pilot to control the aircraft’s pitch by adjusting the angle of the horizontal stabilizer, thus influencing the nose-up or nose-down attitude.
The aileron is another essential component of the empennage, contributing significantly to roll control. Positioned on the outer portion of each wing, ailerons work differentially – when one goes up, the other goes down, causing the aircraft to roll about its longitudinal axis. This controlled rolling motion is crucial for banking and turning during flight.
For fine-tuning the aircraft’s performance, the empennage includes trim tabs on the control surfaces. These small, adjustable surfaces aid in balancing control forces, reducing the pilot’s workload and ensuring a smoother flying experience. Trim tabs are particularly valuable during extended flights, allowing for precise adjustments to maintain the desired attitude.
It’s important to note that the design and configuration of the empennage can vary across different aircraft types. For instance, some aircraft may feature a T-tail configuration, where the horizontal stabilizer is mounted on top of the vertical stabilizer. This design offers certain aerodynamic advantages, such as reducing the impact of the turbulent airflow from the fuselage.
How the empennage design affects aircraft performance characteristics
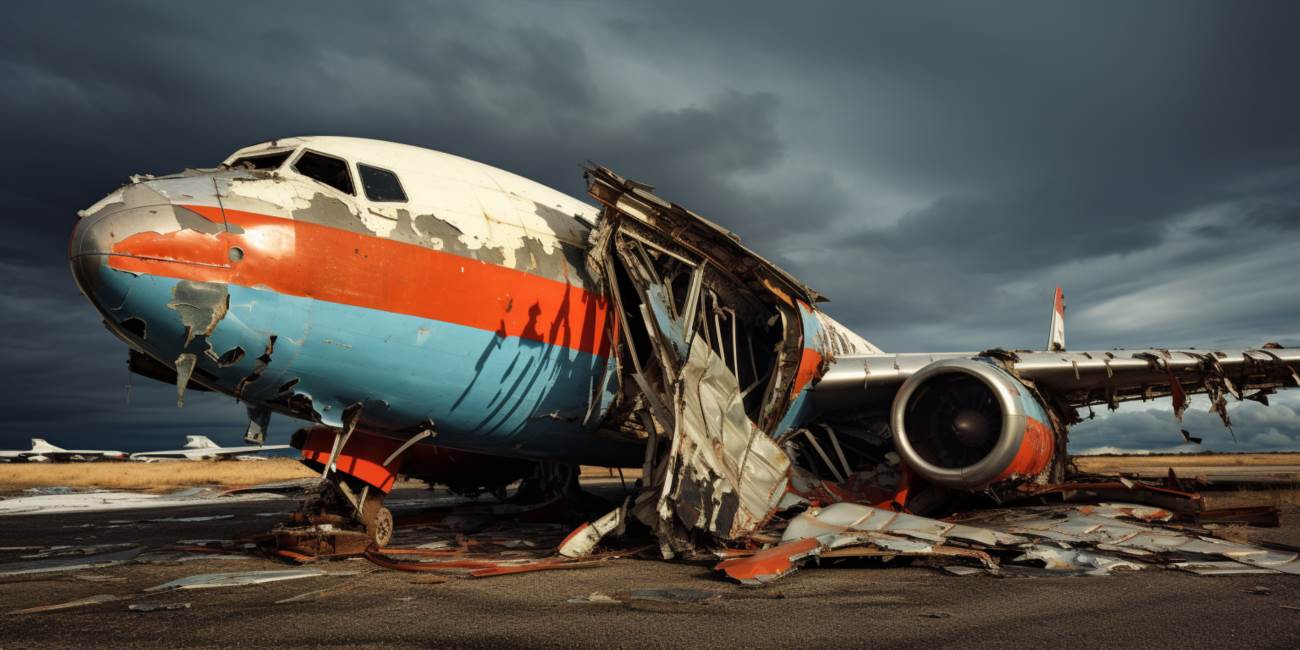
The empennage, also known as the tail assembly, plays a pivotal role in shaping an aircraft’s aerodynamics and overall performance. Its design significantly influences crucial aspects such as lift, drag, stability, and control.
One key element in the empennage design is the horizontal stabilizer, which counteracts the aircraft’s natural tendency to pitch nose-up. This component, often paired with an elevator for pitch control, contributes to the overall stability of the aircraft during flight. The efficiency of the horizontal stabilizer is paramount in maintaining a balanced and controlled flight profile.
Moreover, the vertical stabilizer, commonly equipped with a rudder for control, addresses the aircraft’s tendency to yaw. The judicious design of the vertical stabilizer not only aids in directional control but also influences the overall aerodynamics by minimizing adverse yaw effects.
The size and shape of the empennage components directly impact the distribution of lift and drag across the aircraft. The horizontal and vertical stabilizers contribute to the overall aerodynamic forces acting on the aircraft, affecting its lift-to-drag ratio. A well-designed empennage enhances the aircraft’s efficiency in generating lift while minimizing drag.
Consideration of control surfaces on the empennage, such as elevators and rudders, is vital for responsive and effective flight control. These surfaces, through their dynamic interaction with the airflow, influence the aircraft’s pitch and yaw, directly impacting its control responsiveness. Efficient control surfaces contribute to a more agile and maneuverable aircraft.
Additionally, the empennage’s impact on drag cannot be overstated. A well-designed tail assembly minimizes parasitic drag, enhancing the overall aerodynamic efficiency of the aircraft. This reduction in drag not only improves fuel efficiency but also contributes to higher speeds and better overall performance.
Proper empennage maintenance for continued airworthiness
Proper empennage maintenance is a critical aspect of ensuring the continued airworthiness of an aircraft. The empennage, or tail section, plays a pivotal role in the stability and control of the aircraft, making routine inspections, repairs, and control surfaces checks indispensable for safe operations.
Regular inspections are the cornerstone of empennage maintenance. These assessments involve a meticulous examination of the tail section, focusing on structural integrity, component functionality, and overall condition. Inspections should adhere to manufacturer guidelines and aviation regulatory standards to guarantee thorough evaluations.
During these inspections, technicians pay close attention to potential stress points, corrosion, and any signs of wear and tear. The objective is to identify issues before they escalate, ensuring preemptive repairs can be carried out to maintain optimal airworthiness. This proactive approach is essential for preventing catastrophic failures during flight.
Efficient repairs are paramount once issues are detected. Whether addressing structural damage, control surface malfunctions, or other abnormalities, prompt and precise repairs are crucial. Technicians must follow approved repair procedures and use certified materials to uphold the aircraft’s original design and specifications.
Moreover, control surfaces checks are an integral part of empennage maintenance. These checks involve a comprehensive review of the rudder, elevators, and other control surfaces to confirm their proper functioning. Any deviation from the expected range of motion or irregularities can be indicative of underlying problems, necessitating immediate attention and potential repairs.
Utilizing a structured approach to control surfaces checks involves systematic assessments of each component’s hinges, actuators, and connecting points. This meticulous examination ensures that the aircraft’s control systems operate seamlessly, contributing to the overall safety and performance of the flying machine.