Modern aircraft must endure a wide range of meteorological conditions throughout their operational life, including extreme temperatures, turbulent winds, and precipitation. Each of these factors poses unique challenges to the structural integrity of an aircraft. The structural components need to withstand not only the routine stresses of takeoff, flight, and landing but also the unpredictable forces unleashed by meteorological variations.
Aircraft structural testing involves subjecting the airframe and its components to simulated meteorological conditions in controlled environments. This allows engineers to analyze how different weather scenarios impact the structural performance. The use of advanced testing facilities, such as wind tunnels and environmental chambers, enables researchers to recreate a spectrum of meteorological environments with precision.
The effects of temperature extremes are assessed by exposing the aircraft to both high and low temperature conditions. This is vital as temperature fluctuations can affect the materials used in the aircraft’s construction, leading to expansion, contraction, and potential fatigue. Structural testing in extreme temperatures helps engineers refine designs to ensure optimal performance under diverse meteorological conditions.
Additionally, turbulent winds are simulated to gauge how the aircraft’s structure responds to aerodynamic forces during adverse weather conditions. The ability to withstand gusts and turbulence is critical for passenger comfort and the safety of the aircraft. Engineers carefully examine the aerodynamic stability and structural response under these meteorological challenges.
Another crucial aspect of aircraft structural testing is the evaluation of the impact of precipitation, including rain, snow, and hail. These meteorological factors can lead to corrosion, icing, or increased weight on the aircraft surfaces. Structural components are subjected to simulated precipitation in testing facilities to assess their resilience and durability.
How to test aircraft structure in humid meteorological environment
When testing aircraft structure in humid meteorological environments, engineers face unique challenges that require specialized methodologies. The impact of high humidity on materials and structural integrity necessitates meticulous testing procedures to ensure the safety and reliability of aircraft.
One of the primary considerations in testing aircraft structures in humid conditions is the corrosion resistance of materials. Humidity accelerates the corrosion process, posing a potential threat to the structural components of an aircraft. Testing protocols must, therefore, incorporate assessments of materials’ resistance to corrosion under varying humidity levels.
Non-destructive testing (NDT) methods play a crucial role in evaluating the structural integrity without causing harm to the aircraft. Techniques such as ultrasonic testing, eddy current testing, and thermography enable engineers to identify potential issues like delamination or corrosion in the structure, providing valuable insights into the health of the aircraft.
It is imperative to account for the effects of humidity on composite materials commonly used in modern aircraft construction. High humidity can lead to the absorption of moisture by composites, potentially compromising their structural properties. Testing procedures must include assessments of composite materials under simulated humid conditions to gauge their performance and durability.
Utilizing humidity chambers in testing facilities becomes essential to simulate real-world conditions. These chambers allow engineers to control and manipulate humidity levels, recreating the challenges posed by humid meteorological environments. Testing within these controlled chambers ensures a more accurate evaluation of the aircraft structure’s response to varying humidity levels.
The mechanical properties of materials, including tensile strength and fatigue resistance, can be significantly affected by humidity. Testing protocols must include assessments of these properties under humid conditions to determine the material’s performance over the lifespan of the aircraft.
Incorporating sensor technologies is crucial for real-time monitoring during testing. These sensors can measure environmental conditions, including humidity levels, allowing engineers to correlate data with structural responses. This integration of technology enhances the precision of the testing process and provides a comprehensive understanding of the aircraft’s behavior in humid environments.
Collaboration between meteorologists and aviation engineers is essential in developing accurate testing parameters. Meteorological data, including humidity variations in different geographical locations, should be integrated into testing protocols. This collaborative approach ensures that aircraft structures are tested under conditions representative of their operational environments.
Testing aircraft structure in humid meteorological environments is a multidimensional process that requires a combination of advanced technologies, simulation chambers, and collaborative efforts. As aviation continues to evolve, ensuring the resilience of aircraft structures under diverse environmental conditions remains paramount for safety and reliability.
Necessary aircraft structure examinations in windy conditions
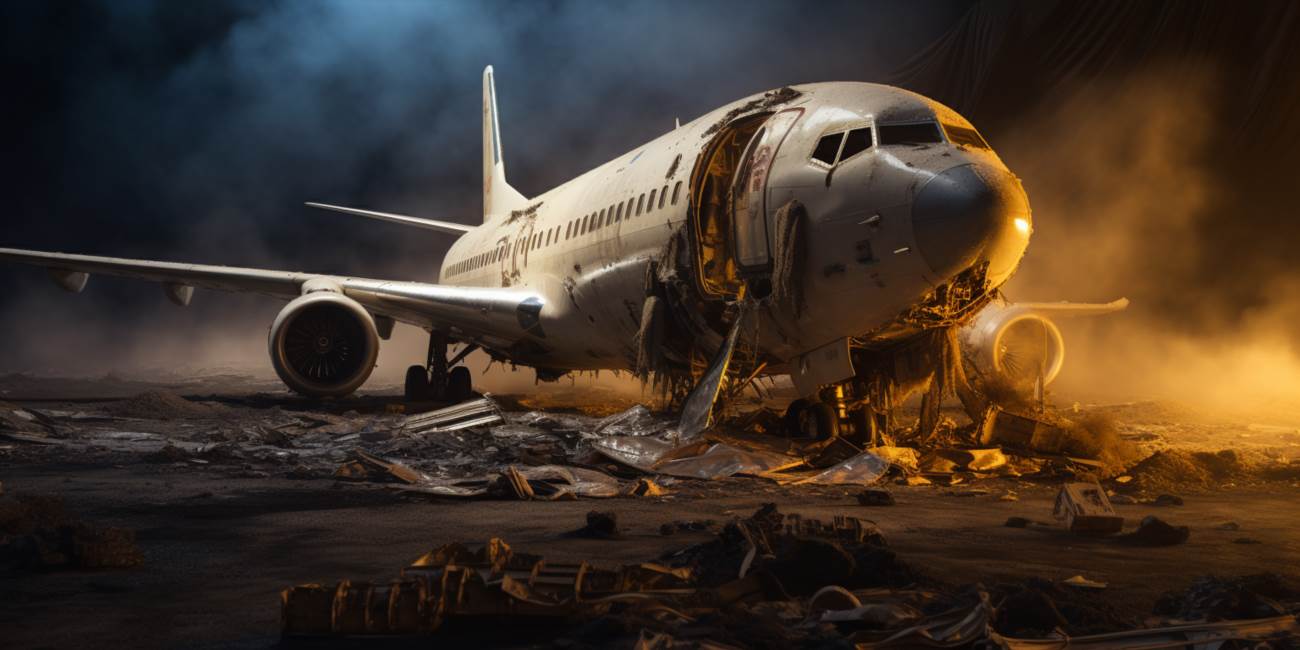
Aircraft structure examinations become particularly crucial when facing challenging weather conditions, especially in gusty, blustery, blowy, breezy, or draughty conditions. These environmental factors pose unique challenges to the integrity and safety of an aircraft, necessitating thorough inspections and assessments.
In gusty conditions, where sudden and strong wind fluctuations are prevalent, aircraft structures are subjected to varying loads that can impact their stability. The wings, fuselage, and tail components must undergo rigorous inspections to ensure they can withstand the dynamic forces exerted during takeoff, flight, and landing.
Blustery conditions, characterized by violent and forceful winds, demand a meticulous examination of all external surfaces. Critical areas such as the wings’ leading edges, where airflow is disrupted, require special attention to detect any potential damage or wear. Structural engineers employ advanced techniques, including non-destructive testing, to identify hidden defects that might compromise the aircraft’s structural integrity.
Similarly, during blowy conditions, when continuous strong winds prevail, it is imperative to inspect the control surfaces, hinges, and attachment points. Rigorous checks on the ailerons, elevators, and rudders are essential to ensure their proper functioning under the sustained aerodynamic forces experienced during flight.
Operating an aircraft in breezy conditions presents challenges related to lateral stability and control. Structural examinations focus on the wing structure and its connections to the fuselage, aiming to identify any signs of fatigue, corrosion, or stress concentrations. Comprehensive assessments are conducted to guarantee the aircraft’s capability to maintain stable flight attitudes.
Lastly, in draughty conditions, where air currents infiltrate the aircraft interior, inspections extend beyond external surfaces. Seals, joints, and access panels are scrutinized to prevent any compromise in the pressurization system. Ensuring a draught-free interior is vital for both passenger comfort and the overall safety of the flight.
Aviation authorities and maintenance crews prioritize these examinations, recognizing the critical role they play in preserving the structural soundness of aircraft during challenging weather conditions. The commitment to regular and thorough assessments enhances safety standards, mitigating potential risks associated with gusty, blustery, blowy, breezy, and draughty environmental factors.
Testing aircraft construction extremely hot weather
Testing aircraft construction in extremely hot weather poses a formidable challenge, pushing the limits of engineering and design. The aviation industry, ever on the quest for innovation and safety, subjects aircraft to trials in the most torrid conditions imaginable. It’s a crucible where the resilience of materials and the efficiency of cooling systems are scrutinized under the relentless assault of baking temperatures.
In the realm of aviation, where precision and reliability are paramount, exposing aircraft to the elements of boiling heat becomes a crucial step in ensuring their performance under extreme conditions. The tarmac becomes a testing ground where the fusion of cutting-edge technology and the ferocity of broiling temperatures meld to form a crucible for aeronautical endurance.
The fuselage, wings, and critical components are subjected to the scorching heat, where the effectiveness of insulation materials is tested in the face of the blistering sun. It’s a relentless examination of the aircraft’s ability to withstand not only the soaring temperatures but also the consequential thermal expansion and contraction that occurs during flight and on the ground.
One crucial aspect of these trials is the evaluation of cooling systems. As the mercury rises, the torrid conditions can push engines to their limits. Cooling mechanisms, both passive and active, are assessed to ensure optimal performance when the surroundings are nothing short of baking. The ability to dissipate heat efficiently is not just a matter of comfort for passengers and crew but a critical factor in maintaining the aircraft’s structural integrity.
Materials play a pivotal role in these trials. The exposed surfaces of the aircraft must endure the boiling temperatures without compromising their structural integrity. Composite materials, alloys, and coatings undergo meticulous scrutiny to ascertain their resistance to the broiling conditions that aircraft might encounter in diverse global climates.
It’s not just the physical components that are tested but also the electronic systems. Avionics, subjected to blistering heat, must demonstrate their resilience to extreme temperatures, ensuring that they function seamlessly even in the most challenging operational environments.
In essence, the testing of aircraft construction in torrid, baking, boiling, broiling, and blistering conditions is a testament to the commitment of the aviation industry to safety and reliability. Each trial is a step towards ensuring that aircraft can navigate the skies with unwavering performance, regardless of the atmospheric challenges they might encounter.