The Dreamliner’s alternative name, the Boeing 787, underscores its significance in Boeing’s aircraft lineup. Known for its distinctive features, this marvel of engineering is often referred to as the “787” in aviation circles, a designation that encapsulates its technological prowess and futuristic design.
One of the standout features of the Boeing 787 is its extensive use of composite materials in its construction. This not only enhances fuel efficiency but also contributes to a lighter and more durable airframe. The integration of these advanced materials marks a paradigm shift in aircraft manufacturing, paving the way for a more sustainable and eco-friendly era in aviation.
The Dreamliner’s fuel efficiency is a game-changer in the industry, driven by advanced engine technology and aerodynamics. The aircraft boasts impressive fuel economy, reducing both operating costs for airlines and environmental impact. This aligns with the industry’s growing emphasis on sustainability and a commitment to greener aviation practices.
Passenger experience takes center stage aboard the Boeing 787. The spacious and well-lit cabin design creates a more comfortable and enjoyable journey for travelers. The large windows, dimmable at the touch of a button, offer breathtaking views and contribute to an open and airy atmosphere within the aircraft.
Moreover, the 787’s quiet engines redefine the in-flight experience, minimizing noise levels and enhancing overall comfort. This focus on passenger well-being extends to the advanced air filtration system that ensures a cleaner and healthier cabin environment, a crucial aspect in the context of global health considerations.
Efficiency is not limited to the aircraft’s performance alone. The Dreamliner incorporates state-of-the-art technology systems, including advanced avionics and connectivity features. This translates to improved communication, navigation, and overall operational efficiency, meeting the demands of the modern aviation landscape.
In terms of market impact, the Boeing 787 has seen widespread adoption by major airlines worldwide. Its versatility, range, and fuel efficiency make it a preferred choice for long-haul routes, connecting distant destinations with unprecedented efficiency.
As we look ahead, the Boeing 787 Dreamliner stands as a symbol of progress in aviation, embodying the fusion of technology and passenger-centric design. Its alternative name, the Boeing 787, encapsulates the essence of a new era in air travel, where innovation takes flight.
Dreamliner provides higher cabin pressure and humidity
The Dreamliner has revolutionized air travel with its emphasis on passenger comfort, introducing a groundbreaking approach to cabin pressure and humidity.
One of its most remarkable features is the enhanced cabin pressure, maintained at approximately 6,000 feet during flight. This is a significant departure from the standard cabin altitude of around 8,000 feet in traditional aircraft. By simulating a lower altitude, passengers experience reduced fatigue and the effects of jet lag are minimized. This difference is achieved through advanced composite materials used in the aircraft’s construction, allowing for a more pressurized cabin without compromising structural integrity.
Humidity levels aboard the Dreamliner are another standout aspect. Typically, air travel cabins tend to have low humidity levels, causing discomfort such as dry skin and dehydration. However, the Dreamliner employs humidity control systems that maintain the moisture level at around 15%, significantly higher than the industry standard. This improved humidity contributes to a more pleasant flying experience, helping passengers feel more refreshed upon arrival.
A higher humidity level also reduces the overall impact of jet lag, as it helps the body maintain a more natural state of hydration throughout the flight. Combined with the lower cabin pressure, this feature stands as a testament to the Dreamliner’s dedication to passenger well-being.
Comparison | Standard Aircraft | Dreamliner |
---|---|---|
Cabin Pressure | Approx. 8,000 feet | Approx. 6,000 feet |
Humidity Level | Industry Standard | Around 15% |
These innovations in cabin pressure and humidity represent a significant leap forward in air travel comfort. Passengers on the Dreamliner can now arrive at their destinations feeling more refreshed and less fatigued, setting a new standard for the industry.
Lower operating costs thanks to advanced composite materials
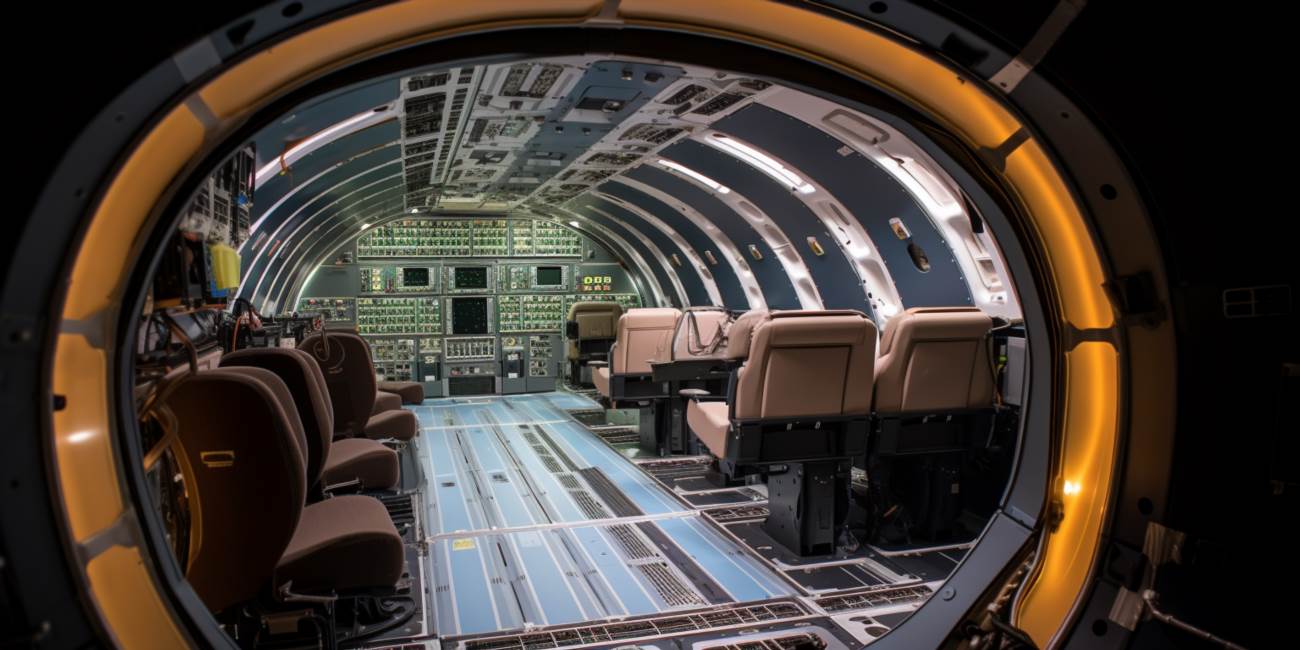
Advanced composite materials have revolutionized various industries, offering a myriad of benefits, particularly in the realm of transportation. One of the most compelling applications of composites is in the manufacturing of aircraft components, including engine parts. The utilization of these cutting-edge materials has not only contributed to the creation of lighter and more durable structures but has also led to significant reductions in operating costs.
The key to understanding the economic advantages lies in the relationship between composite materials and enhanced fuel efficiency. Traditional materials, such as aluminum, which were once prevalent in aircraft construction, are being replaced by composites due to their superior strength-to-weight ratio. This translates into a reduction in the overall weight of the aircraft, subsequently lowering the amount of fuel required for operation.
Imagine an aircraft with components made from composite materials, where the engine itself incorporates these advanced substances. The lighter weight not only enables more efficient fuel consumption but also enhances the overall performance of the engine. With reduced mass to propel, the engine can operate with greater ease, leading to improved fuel efficiency and, consequently, lower operating costs.
Moreover, the durability of composite materials plays a pivotal role in the long-term savings for operators. These materials exhibit excellent resistance to corrosion and fatigue, reducing the frequency of maintenance and replacement of engine components. The result is not only a decrease in downtime but also a substantial cut in maintenance expenses, contributing further to the overall savings achieved through the use of advanced composite materials.
To illustrate the impact of this shift in materials, consider the following
Material | Weight | Corrosion Resistance | Fatigue Resistance |
---|---|---|---|
Aluminum | High | Moderate | Moderate |
Composite | Light | High | High |
The table highlights the comparative advantages of composite materials over traditional alternatives. The lightweight nature, coupled with superior resistance to corrosion and fatigue, positions composites as the material of choice for achieving optimal fuel efficiency, enhancing engine performance, and ultimately realizing substantial operating cost savings.
Composite wings and horizontal stabilizers boost performance
Composite materials have revolutionized the aerospace industry, particularly in the design and construction of aircraft wings and horizontal stabilizers. These advanced materials, often a blend of carbon fiber, epoxy resin, and other high-strength components, contribute significantly to enhancing overall performance and efficiency in flight.
One of the primary advantages of composite wings lies in their ability to provide a remarkable balance between strength and weight. The use of lightweight yet durable materials reduces the structural weight of the aircraft, resulting in improved performance metrics. The decreased weight directly translates into enhanced speed, allowing the aircraft to reach higher velocities while maintaining stability.
The aerodynamic properties of composite wings play a pivotal role in optimizing lift and minimizing drag. The carefully engineered shape and composition of these wings contribute to efficient flight dynamics. By minimizing drag, composite wings help reduce the resistance that an aircraft faces during forward motion, ultimately contributing to better fuel efficiency and increased speed.
Horizontal stabilizers, often overlooked but crucial components, also benefit from composite materials. These stabilizers, situated at the tail of an aircraft, play a vital role in maintaining stability and controlling pitch during flight. The lightweight nature of composites used in these stabilizers ensures that they can effectively perform their functions without adding unnecessary weight, thus optimizing performance.
As aircraft continue to push the boundaries of performance and speed, the role of composite materials becomes even more pronounced. The interplay between lightweight structures, advanced aerodynamics, and precision engineering contributes to an aircraft’s ability to achieve optimal performance parameters. The evolution of composite wings and horizontal stabilizers reflects a commitment to pushing the limits of flight capabilities.
Advantages of Composite Wings and Stabilizers | Impact on Aircraft Performance |
---|---|
1. Lightweight | Reduces structural weight, enhancing overall performance and speed. |
2. Aerodynamic Efficiency | Optimizes lift, minimizes drag, and improves fuel efficiency during flight. |
3. Stability | Contributes to aircraft stability and control, particularly through composite horizontal stabilizers. |